Expert Solutions for Streamlined Product Packaging Equipment Upkeep and Repair Providers
Professional options that utilize anticipating upkeep strategies and utilize IoT modern technology use a path to minimize unexpected downtime and minimize costs. As organizations seek to raise their functional effectiveness, one need to think about how these innovative methods can change maintenance techniques.
Predictive Upkeep Strategies
In the world of product packaging devices upkeep, anticipating upkeep strategies have actually emerged as a transformative method to minimizing downtime and boosting operational effectiveness. Predictive upkeep relies on condition-monitoring devices and IoT-enabled sensing units that constantly examine the operational state of equipment.
The implementation of predictive upkeep provides a number of advantages. First, it enables companies to change from responsive to positive maintenance techniques, decreasing the regularity and seriousness of tools failures (packaging equipment repair services). This approach not just prolongs the lifespan of equipment but additionally optimizes the scheduling of upkeep jobs, guaranteeing that sources are utilized effectively and effectively. Predictive upkeep adds to set you back financial savings by lowering the demand for emergency situation repair services and decreasing manufacturing interruptions.
Strategically, business that take on anticipating upkeep acquire a competitive side by enhancing tools reliability and total performance. As technology remains to advance, the integration of predictive upkeep strategies right into product packaging tools upkeep programs will progressively become a common method, driving lasting functional improvements.
Effective Repair Service Procedures
Improving the fixing process is crucial for keeping the functional efficiency of packaging equipment. Reliable repair service methods make sure marginal downtime, prolong equipment life expectancy, and enhance production schedules. A structured strategy starts with developing clear repair service guidelines, which include step-by-step instructions customized to every particular equipment type. These standards need to be conveniently available to maintenance employees and consistently upgraded to integrate the most up to date technological advancements and sector criteria.
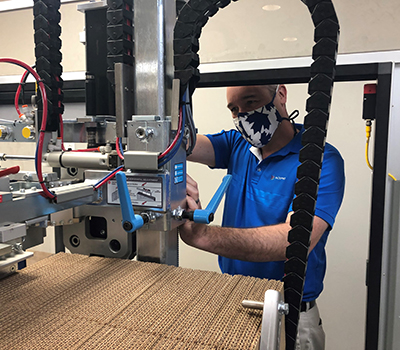
Educating upkeep groups in these protocols is similarly essential. Routine workshops and hands-on training sessions encourage personnel to carry out repair services swiftly and precisely. Fostering a culture of constant renovation motivates responses from professionals, leading to enhancements in repair service methods and protocols.
Advanced Diagnostic Tools
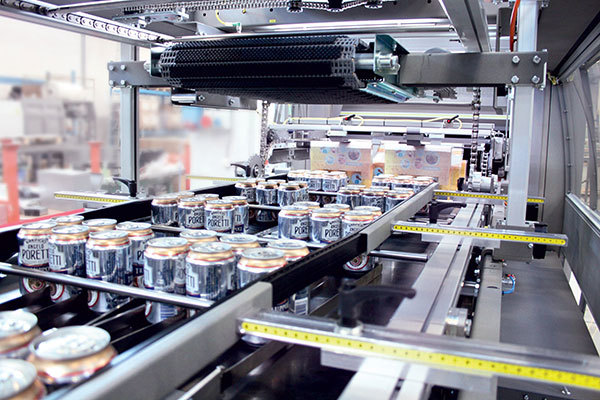
Advanced diagnostic devices give thorough understandings right into the condition of packaging equipment. As an example, thermal imaging electronic cameras can find overheating parts, permitting for timely treatment. Vibration analyzers monitor machinery resonances, identifying variances that may indicate mechanical mistakes, while ultrasonic detectors can pinpoint air leakages or electric discharges that are not visible to the nude eye. These tools jointly contribute to a more enlightened and precise maintenance technique.
Additionally, incorporating advanced diagnostic devices into official website maintenance methods allows data-driven decision-making. The collected information aids in predicting equipment failings and planning targeted repair services. Services can assign resources extra effectively, reduce upkeep expenses, and enhance the general reliability of their packaging systems.
Training and Skill Growth
The performance of sophisticated diagnostic devices is substantially enhanced when combined with detailed training and ability development for upkeep workers. Training programs tailored to the specific requirements of packaging equipment are vital.
Ability growth efforts can take different types, including workshops, certification courses, on-the-job training, and cross-training amongst staff member. Stressing constant understanding ensures that specialists are abreast of the current technical improvements and upkeep methods. Additionally, investing in ability advancement cultivates a culture of development and analytic, making it possible for upkeep teams to resolve devices problems proactively.
Furthermore, trained workers add to minimizing downtime and enhancing tools performance, eventually leading to raised operational efficiency and cost savings. Establishing a structured training plan, straightened with organizational objectives, guarantees that the workforce is experienced and confident in maintaining high requirements of devices treatment. This critical approach to training and ability advancement is essential in accomplishing streamlined upkeep procedures in the packaging industry.
Leveraging IoT and Automation
In today's quickly developing packaging iot, automation and market are transforming upkeep techniques, providing unmatched levels of performance and accuracy. By integrating IoT-enabled sensing units and gadgets, product packaging tools can currently communicate real-time information regarding functional condition and possible mistakes. This connectivity enables predictive upkeep, where problems are recognized and attended to before they intensify right into costly break downs, therefore reducing downtime and expanding devices lifespan.
Automation further enhances these capabilities by browse around this site automating regular upkeep jobs and diagnostics. With the implementation of automated systems, companies can improve their maintenance routines, minimizing manual treatment and the margin for human mistake. Automated notifies and reports produced by IoT gadgets make sure maintenance groups are always informed, advertising an aggressive approach to tools care.
In addition, the combination of IoT and automation facilitates smooth data analysis, enabling better decision-making procedures. By harnessing data analytics, companies can obtain insights right into devices performance fads, optimize resource allotment, and enhance overall operational effectiveness. This technical synergy not only lowers maintenance prices yet also boosts efficiency and dependability in packaging procedures. As the sector remains to progress, leveraging IoT and automation is vital for maintaining a competitive side in equipment upkeep.
Final Thought
The combination of anticipating maintenance methods, reliable fixing protocols, and advanced diagnostic tools significantly improves packaging equipment repair and maintenance services. By leveraging IoT and automation, potential failures can be prepared for and dealt with proactively, therefore lowering downtime and prices. Structured training and ability development for service technicians better guarantee the swift implementation of essential repair work. This detailed strategy not only prolongs the life-span of equipment however also boosts performance and integrity, eventually enhancing functional efficiency in packaging procedures.
In the realm of product packaging tools upkeep, anticipating upkeep methods have actually arised as a transformative approach to minimizing downtime and improving functional performance.Utilizing innovative diagnostic devices is essential in boosting the maintenance and repair of product packaging tools. In enhancement, investing in ability growth promotes a culture of next technology and analytical, enabling maintenance teams to deal with devices issues proactively.
Automated reports and signals generated by IoT devices guarantee maintenance teams are constantly notified, promoting an aggressive approach to equipment care.
The combination of anticipating maintenance techniques, reliable repair work methods, and advanced diagnostic tools substantially boosts product packaging equipment upkeep and repair services.